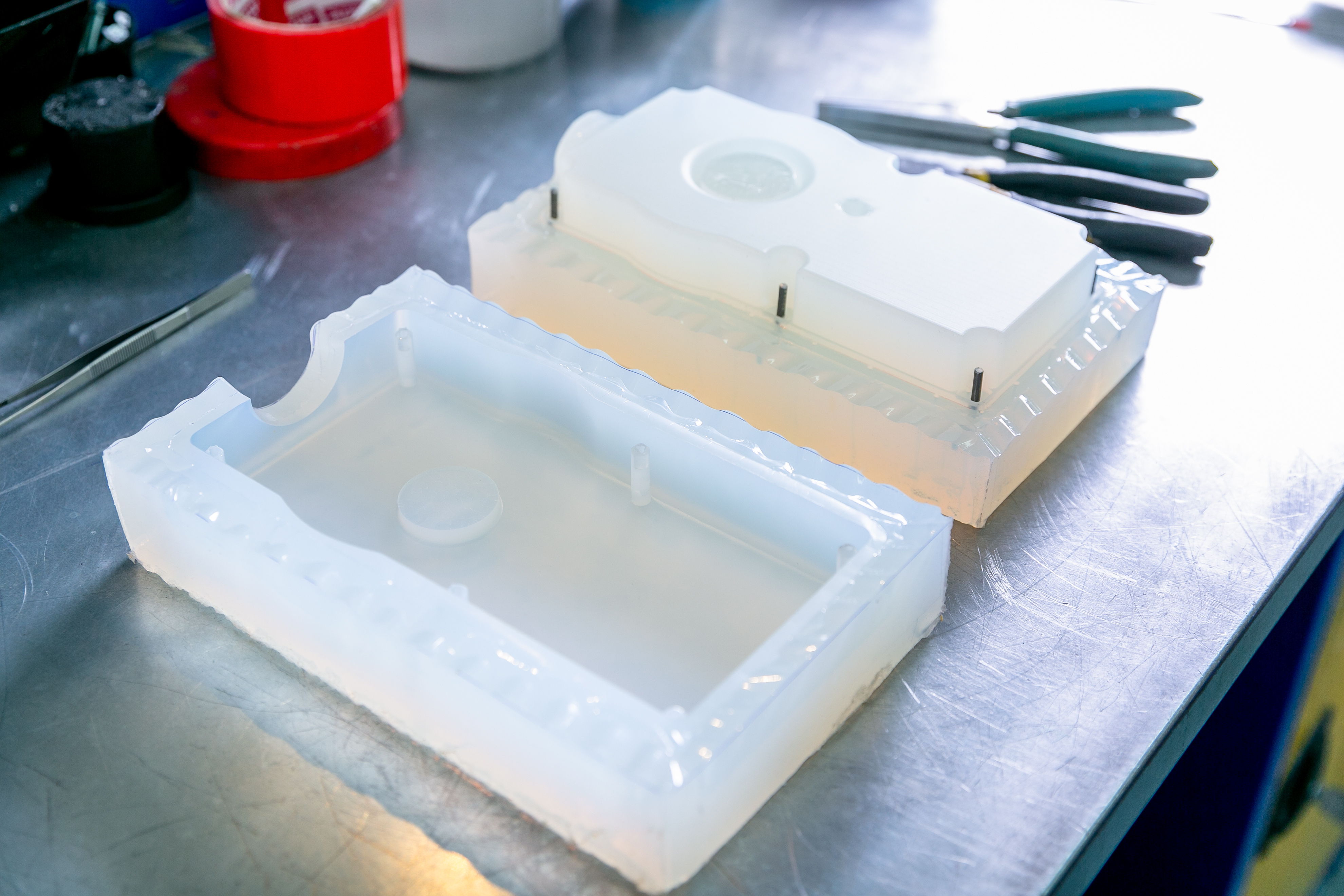
製造業において、小ロット生産の効率化や試作コストの削減は大きな課題です。特に、射出成形やダイキャストを用いた従来の製造プロセスでは、金型の製作コストが高く、短納期対応が難しい場合があります。そこで注目されているのが「真空注型」という技術です。真空注型は、3Dプリンターやマスター型を活用して、短期間で高品質な試作品や少量生産を可能にする手法です。この技術は、樹脂部品やゴム製品の試作・小ロット生産に最適であり、開発スピードの向上やコスト削減を実現します。この記事では、真空注型の仕組み・メリット・活用事例を詳しく解説し、製造業における小ロット生産の最適解としての可能性を探ります。
真空注型とは
真空注型とは、シリコン型を用いてウレタン樹脂やゴムなどの材料を成形する製造方法です。主に試作や小ロット生産に適しており、コストを抑えながら高精度な製品を短納期で製造できることが特徴です。特に、金型を必要としないため、射出成形と比較して初期投資が少なく、開発スピードを大幅に短縮できます。
真空注型のプロセスと使用材料
真空注型の基本的なプロセスは、まず3DプリンターやCNC加工機でマスター型を作成することから始まります。次に、そのマスター型をシリコンゴムで覆い、硬化させることでシリコン型を作成します。その後、真空環境下でウレタン樹脂やエポキシ樹脂を注入し、硬化させることで成形品が完成します。最後に、型から取り出し、仕上げ作業を行います。
使用される材料には、耐熱性や耐衝撃性を求められる部品に適したウレタン樹脂や、高強度なエポキシ樹脂、弾性が求められるシリコンゴムなどがあります。
他の製造方法(射出成形・3Dプリンターなど)との比較
真空注型は、初期投資が少なく、射出成形に比べて金型製作の必要がないため、小ロット生産に向いています。一方で、大量生産には向いておらず、シリコン型の耐久性も射出成形用の金型と比べると低いです。また、3Dプリンターによる製造と比較すると、真空注型のほうが寸法精度や機械的強度の面で優れています。
真空注型のメリットとデメリット
メリット:短納期・コスト削減・高精度
真空注型の大きなメリットの一つは、短納期で試作品を製作できることです。シリコン型は短期間で作成できるため、金型製作のリードタイムを削減し、迅速な製造が可能になります。また、金型が不要なため、初期投資を抑えることができ、小ロット生産においてコスト削減につながります。さらに、射出成形に近い精度で製品を成形できるため、デザインや機能の検証にも適しています。
デメリット:大量生産には不向き
一方で、シリコン型の耐久性には限界があり、通常30~50ショット程度で劣化してしまいます。そのため、大量生産を目的とした製造には適しておらず、量産向けの製品には射出成形などの方法が選ばれることが一般的です。また、1個あたりの生産コストは中ロット以上になると射出成形よりも割高になることがあります。
真空注型を活用すべきケースとは?
真空注型は、試作品の製作や市場テスト向けの少量生産に最適です。特に、デザインや機能の検証を行うための試作部品や、小ロットでの製品開発を行う際には、高いコストパフォーマンスを発揮します。また、新製品の市場テストやプレ販売を行う際にも、短期間で製品を用意できるため有効です。
真空注型の活用事例と実績
小ロット生産・試作品開発の事例
真空注型は、さまざまな業界で活用されています。例えば、家電メーカーでは、新型リモコンの試作に使用されることがあります。また、自動車部品メーカーでは、エアコンダクトのプロトタイプ製作に活用されるケースが増えています。医療機器メーカーでは、患者ごとに異なるフィット感が求められるシリコン製パーツの試作に利用されています。
自動車・医療・家電業界での活用例
自動車業界では、内装パーツやスイッチ類の試作に真空注型が活用されています。医療業界では、患者ごとに異なる形状が求められるシリコン製部品の製作に使用されています。家電業界では、新製品の開発スピードを向上させるために、試作品の製作に活用されることが一般的です。
コスト削減・リードタイム短縮の実績
真空注型を導入することで、試作コストを従来の30%削減し、リードタイムを50%短縮できた事例もあります。金型不要の製造方法のため、開発段階のコストを抑えながら、迅速に製品を市場に投入することが可能になります。
真空注型に適した製品
真空注型は、プラスチック製試作品、ゴム部品、透明樹脂部品の製作に適しています。特に、家電製品や自動車部品の試作、光学製品のランプカバーなど、高い精度が求められる分野で活用されています。
ダイキャスト・簡易金型・石膏鋳造との組み合わせ活用
真空注型は、他の製造方法と組み合わせることで、より幅広い製造ニーズに対応することが可能です。例えば、簡易ダイキャストと組み合わせることで、樹脂部品と金属部品を組み合わせた試作や少量生産が可能になります。また、簡易金型と併用することで、試作段階では真空注型を使用し、本生産時には簡易金型による量産に移行することで、コストと納期のバランスを最適化できます。さらに、石膏鋳造と組み合わせることで、金属部品と樹脂部品の試作を並行して進めることができるため、より効率的な開発が実現します。
まとめ
真空注型は、金型が不要でコストを抑えられることから、小ロット生産や試作品製作に適した製造方法です。特に、短納期での製品開発や市場テストにおいて大きなメリットを持ち、自動車、医療、家電など幅広い業界で活用されています。また、ダイキャストや簡易金型、石膏鋳造と組み合わせることで、より柔軟な製造プロセスを実現することが可能です。製造業の生産効率を向上させるために、真空注型の活用をぜひ検討してみてください。